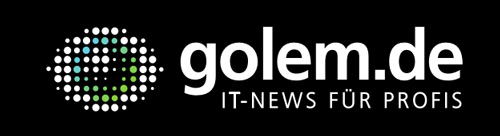
Die Lithium-Ionen-Zelle mit flüssigem Elektrolyt hat noch lange nicht ausgedient. Ein Besuch in Forschung, Crash-Test und Montage bei Porsche und Audi.
Der Schrank, in dem die Batterie liegt, sieht aus wie die Kühlkammer einer Großküche. Doch sie dient in erster Linie dem Brandschutz. „Sollte die Batterie überhitzen und sich entzünden, fluten wir die Kammer mit Wasser“, sagt der Porsche Pressesprecher.
Der Schrank steht im Keller des Porsche Hochvolt-Prüfstands. Der Sportwagenhersteller betreibt drei Prüfstände in seinem Entwicklungszentrum in Weissach. Im Erdgeschoss befinden sich die eigentlichen Messgeräte und Prüfstände mit Antriebssträngen. Man erkennt den Elektromotor und die Achse. Wo eigentlich Räder und Reifen sein sollten, stehen weiße Metallgehäuse, zu denen dicke Schläuche führen. An einem solchen Prüfstand lassen sich sämtliche Fahrsituationen mit einer oder zwei angetriebenen Achsen am Fahrzeug simulieren. Neben Straßenbelag und Fahrweise können die Ingenieure auch die Wetterbedingungen nachbilden. Dabei testen sie hier auch Überlastszenarien der Batterie – während der Fahrt als auch beim Laden. Zudem wird die Interoperabilität unterschiedlicher Schnellladesäulen für alle Exportmärkte getestet. „Die Tests in den Prüfständen liefern früh in der Entwicklung Ergebnisse, die man mit dem Bau von Prototypen erst später ermitteln würde. Wir sind damit schneller und günstiger in der Entwicklung“, sagt der Porsche-Pressesprecher.
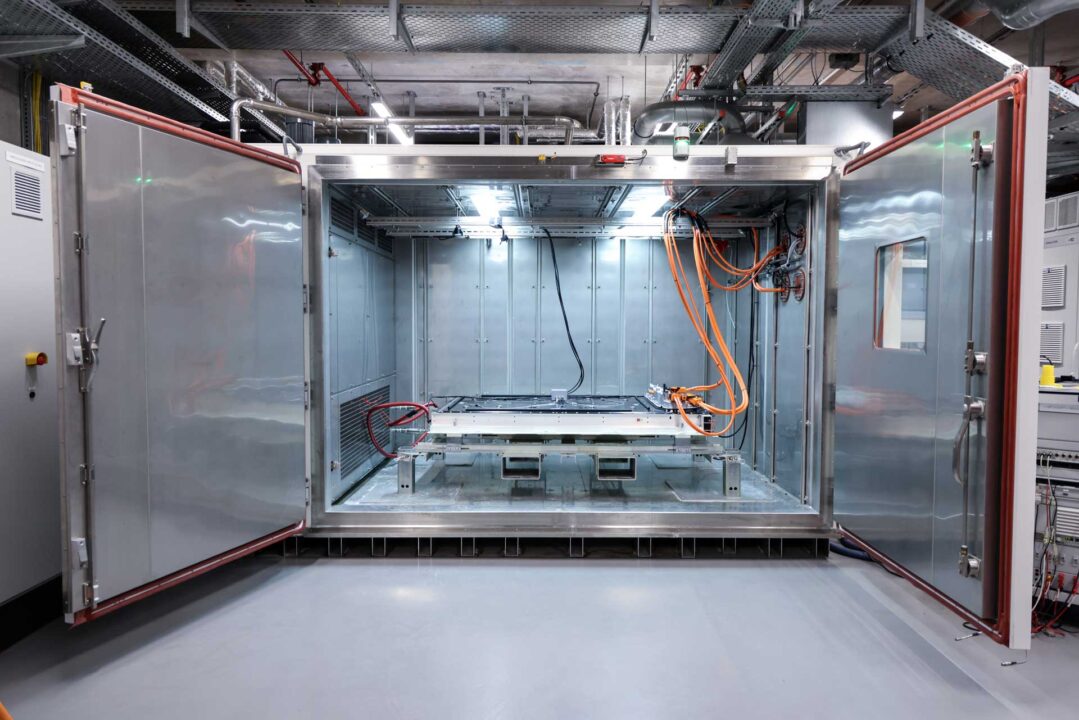
Auf der grünen Wiese
Der moderne Gebäudekomplex steht umgeben von Feldern, Wiesen und Wäldern unweit des baden-württembergischen Ortes Weissach. Der liegt rund 20 km westlich vom Porsche Stammsitz in Stuttgart-Zuffenhausen. Auf den Landstraßen rund um das Entwicklungszentrum herrscht morgens und abends reger Verkehr. Auf dem Campus-artigen Gelände arbeiten 7.500 Menschen, davon rund 80 Prozent in der Entwicklung. Angefangen hat alles 1961 mit einer Fahrdynamikfläche, auf der Ingenieure Runden in Testwagen drehten. Heute umfasst das Gelände 12 Hektar mit eigenem Klima-Windkanal und Crash-Testcenter. Enormer Aufwand für einen verhältnismäßig kleinen Autohersteller, der pro Jahr etwas mehr als 300.000 Autos ausliefert.
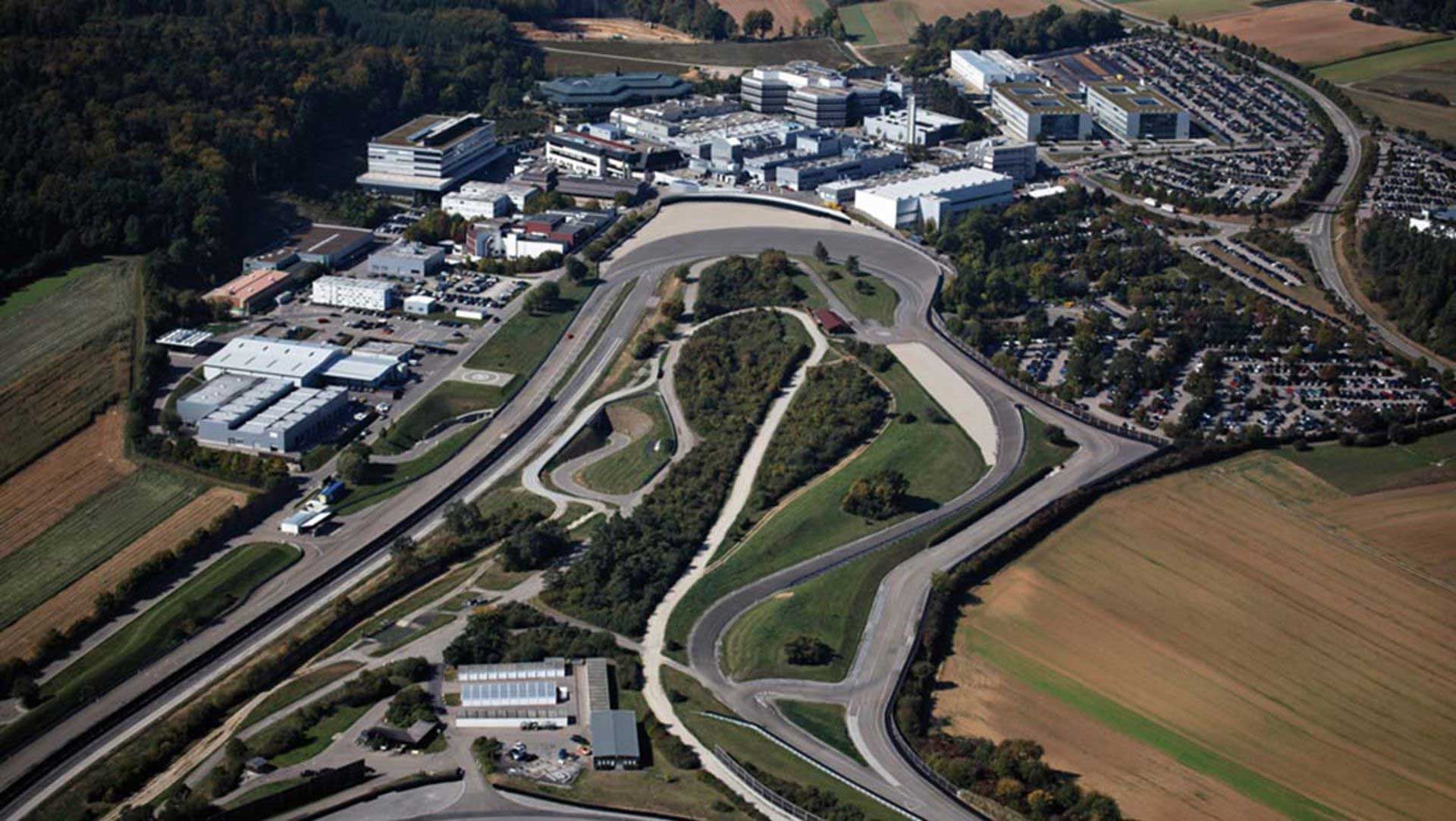
Diverse Zellformate
Elektromobilität kam bei den Porsche-Kunden gut an. Im Jahr 2022 verkaufte Porsche 34.800 elektrische Taycan. Das liegt nur rund 6.000 Stück unter der Zahl des ikonischen Porsche 911. Im Jahr 2023 waren es sogar 40.600 Taycans. In der Batterie stecken 33 Module mit jeweils 12 Pouch-Zellen.
Beim Macan nutzt der Hersteller in zwölf Modulen prismatische Zellen. Bei den hybriden GTS-Modellen setzt Porsche auf zylindrische Zellen. Das sind Hochleistungs-Rundzellen, die man bei der Varta-Insolvenz aus dem Unternehmen herausgekauft und von V4Drive in V4Smart umbenannt hat. Was alle Zellformate eint, es sind Lithium-Ionen-Zellen mit flüssigem Elektrolyten. Auch wenn die Schlagzeilen in Medien oft den Eindruck erwecken, die Feststoffzelle stehe kurz vor ihrem Serieneinsatz, verwenden deutsche Hersteller die etablierte Zellchemie. Mit etwas Ingenieurs-Know-how seien hier noch Sprünge möglich.
Den Beleg liefert Porsche im Frühjahr 2024 mit der zweiten Generation seiner Taycan-Batterie. Auf gleichem Bauraum stehen nun 105 statt 94,4 kWh zur Verfügung. Das steigert die Reichweite um 35 Prozent von 503 auf 678 km. Die Energiedichte steigt um 13 Prozent auf 168,3 Wh pro kg. Die Ingenieure halten einen Zielwert von bis zu 300 Wh pro kg bei der Lithium-Ionen-Zellchemie für möglich. Gleichzeitig sinkt in der zweiten Generation das Gewicht der Batterie von 634 auf 625 kg. Addiert man lediglich das Gewicht der 396 Pouch-Zellen in den 33 Modulen kommt man auf rund 357 kg. Der Rest entfällt auf Leitungen, Kühlplatte, Batteriemanagement, Rahmen und Modul-Hüllen.
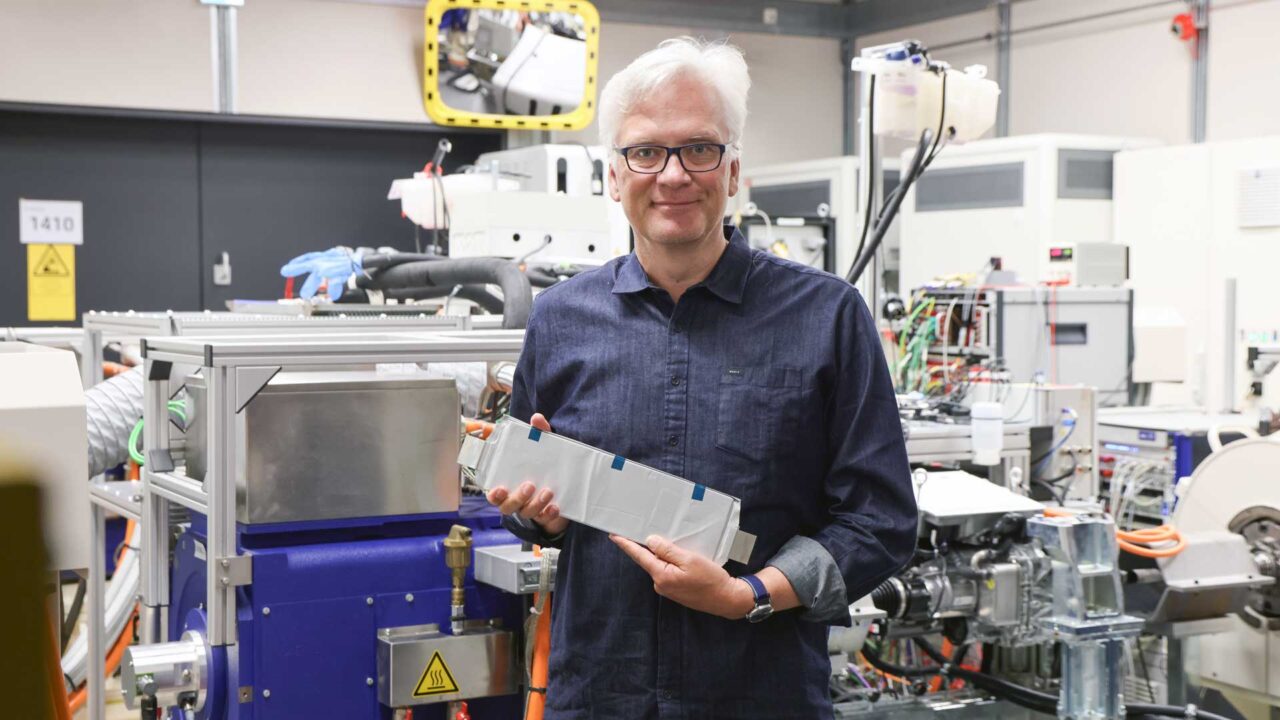
Schnellladen ab 15 Grad Celsius
Die Arbeiten an der neuen Generation gehen zum Teil auf Schwächen der ersten zurück. Ende 2024 rief Porsche weltweit rund 80.000 Taycans zurück. Bei der Hälfte konnte die Fehleranalyse online erfolgen, die anderen 40.000 Fahrzeuge mussten dazu in eine Werkstatt kommen. Im schlimmsten Fall konnte die Hochvoltbatterie überhitzen und sich selbst entzünden.
Porsche hat in der zweiten Generation den grundlegenden Aufbau von Zellen, Modulen, Kühlung und Batteriemanagement überarbeitet. „Wir verwenden eine neue Zellchemie mit geringerem Innenwidersand, eine effizientere Kühlplatte und nutzen Stromschienen, die auf bis zu 1.100 statt 860 Ampere Stromstärke ausgelegt sind“, sagt Matthias Goldsche aus der Porsche Batterieentwicklung.
Die Ingenieure senkten die Startemperatur fürs Schnelladen. In der ersten Generation mussten Zellen mindestens 25 Grad Celsius erreichen, bevor die maximale Ladeleistung freigeschaltet wurde. Das Minimum liegt nun bei 15 Grad Celsius. Danach darf die Ladeleistung bis auf 320 kW steigen. Das bedeutet weniger Energieaufwand für die Vorkonditionierung als auch kürzere Ladepausen außerhalb der Sommermonate. Trotz mehr Batteriekapazität sank die Ladezeit von 21,5 auf 18 Minuten für eine Ladung von 10 bis 80 Prozent.
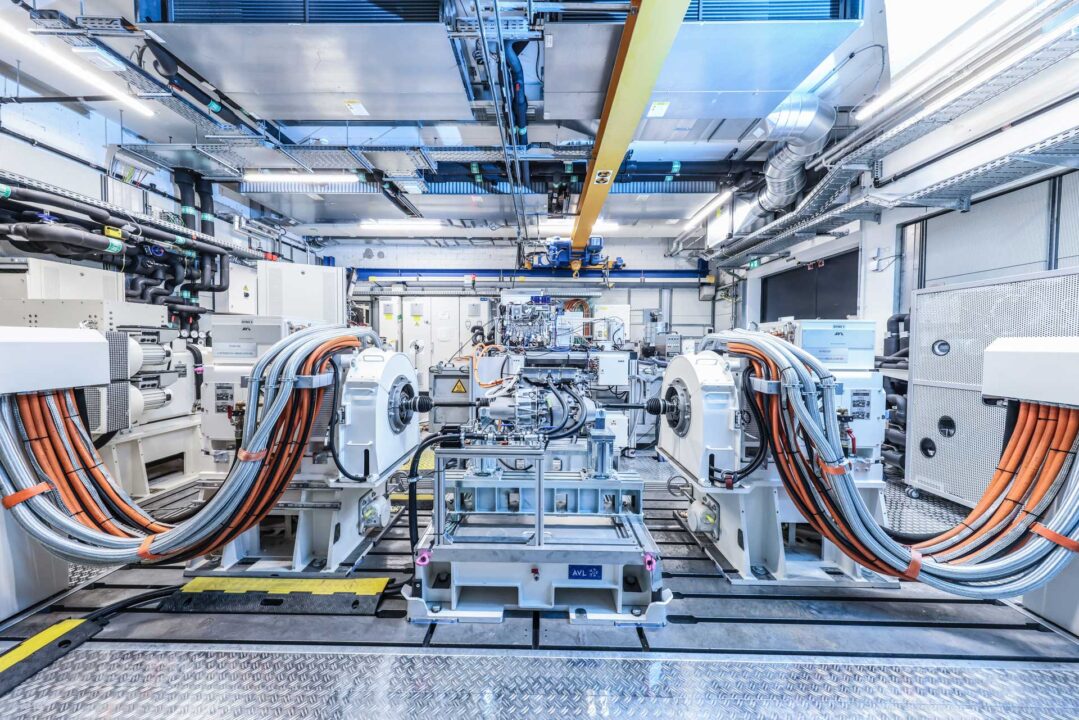
SEI-Schicht ist die „Secret Sauce“
Doch als wichtigste Erfindung bei Lithium-Ionen-Batterien bezeichnet Otmar Bitsche die SEI-Schicht. Bitsche ist die graue Eminenz der Batterie-Forschung bei Porsche und noch in beratender Funktion tätig. SEI steht für Solid Electrolyte Interface (SEI). Diese Schicht bildet sich nach dem Befüllen einer Zelle mit Elektrolyt. Dann reagieren die Salze und Lösungsmittel des Elektrolyts mit dem Anodenmaterial. „Wie stark sich diese Schicht ausprägt, ist die Secret Sauce eines jeden Zellherstellers“, sagt Bitsche. Die SEI-Schicht schützt die Anode vor Korrosion und Degradation, somit ist sie für eine lange Lebensdauer wichtig. Kommt es zu Rissen in der SEI-Schicht, kann sie sich ohne Einfluss von außen neu bilden. Doch dazu benötigt sie flüssigen Elektrolyt. Das führt zu Kapazitätsverlust und steigendem Widerstand in der Zelle.
Neben der kalendarischen Alterung spielte vor allem die Art und Weise der Batterienutzung eine wesentliche Rolle bei der Leistungsfähigkeit. Die Zellen sollten das Temperaturfenster zwischen 30 und 60 Grad Celsius nicht verlassen. Hohe Ladezustände über 90 Prozent, in denen das Auto über längere Zeiträume abgestellt wird, sollte man vermeiden. Das gilt auch für eine dauerhaft sportlich-dynamische Fahrweise. Ausgelegt sind Batterien für mindestens 15 Jahre oder 300.000 km Fahrleistung bei Porsche.
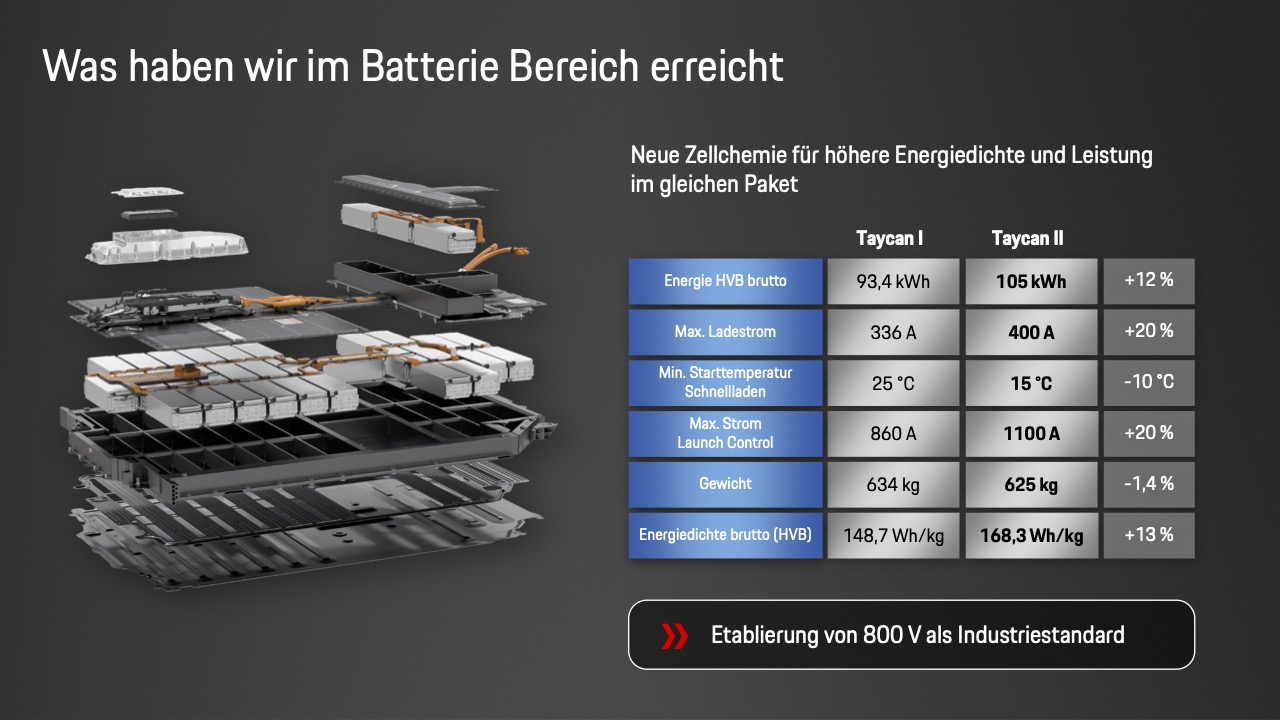
Eigenheiten einer Zelle
Bei der Berechnung der gewünschten Energiekapazität einer Zelle müssen die Entwickler den so genannten Initial Drop berücksichtigen. „Eine Zelle verliert in den ersten zwölf Monaten zwischen zwei und fünf Prozent ihrer Kapazität“, sagt Carlos Alberto Cordova Tineo aus dem Bereich Zellentwicklung der Batterien und Schnellladen bei Porsche. Das sei ein natürlicher Prozess, genau wie die Selbstentladung. „Ein gewisses Maß an Selbstentladung ist vollkommen normal“, so der Ingenieur.
Wird die Batterie geladen steigt mit zunehmendem Füllstand der Widerstand in den Zellen. „Lithium-Ionen finden nicht mehr auf Anhieb einen freien Platz an der Anode“, so Cordova Tineo. Das kann dazu führen, dass Ionen die Energie zur Bildung von Lithiummetall nutzen. Es bilden sich Dendriten, das sind spitze Stachel, die im schlimmsten Fall den Separator durchstoßen und zu einem Kurzschluss in der Batterie führen. Dieses so genannte Lithium Plating will man verhindern, in dem die Ladeleistung mit steigendem Füllgrad (State of Charge) sinkt. Das spüren E-Autofahrer deutlich ab 80 Prozent SoC.
Daher bemühen sich die Ingenieure bei der Weiterentwicklung darum, dass mehr Lithium-Ionen in kürzerer Zeit ihren Platz an der Anode finden. Ein Weg ist die Beimischung von Silizium in das Graphit (Kohlenstoff). „Doch ist die Menge begrenzt, da sich Silizium beim Laden bis zu 300 Prozent ausdehnt, während es bei Graphit nur zehn Prozent sind“, sagt Cordova Tineo.
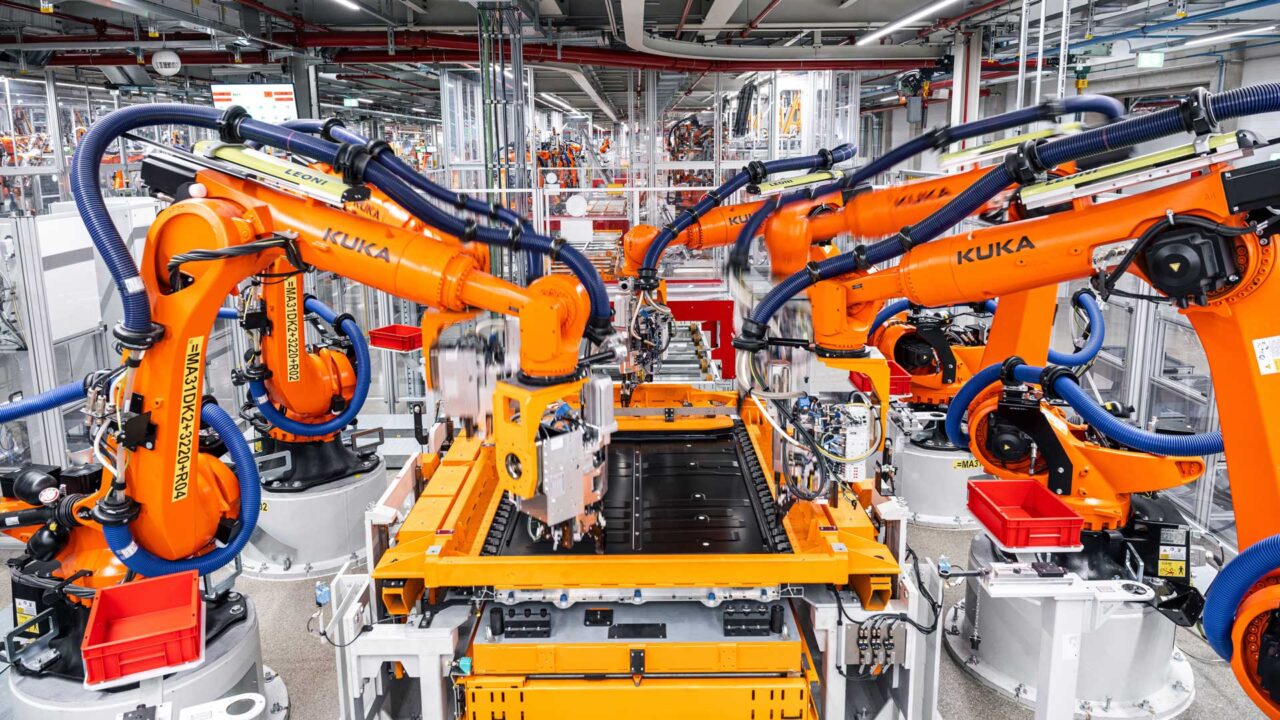
Frühe Fehlererkennung
Ebenfalls eine Konsequenz aus den Erfahrungen mit der ersten Batteriegeneration ist eine frühere Fehlererkennung. Beim elektrischen Macan setzt Porsche auf Mustererkennung und maschinelles Lernen durch Datenanalyse. „Wir werten Daten aus dem Fahrzeug aus und finden mit präventiver Anomaliedetektion Fehler, bevor sie auftreten“, beschreibt es Nora Lobenstein, Leiterin Data Driven Quality. Die Kunden stimmen der laufenden Datenübertragung aus dem Fahrzeug an eine Porsche-Cloud zu. Findet die künstliche Intelligenz Fehler, wird dem Kunden über die My Porsche App ein Service-Termin empfohlen, damit der Fehler behoben werden kann, bevor es zu Einschränkungen für den Kunden kommt. Diese Technik wird auch auf den Taycan ausgeweitet.
Keine Zellfertigung, doch Batteriemontage
Trotz des gewonnenen Know hows steigt Porsche nicht in eine Zellfertigung an. Das übernimmt die VW-Tochter PowerCo. Die erste konzerneigene Zellfertigung befindet sich in Salzgitter im Aufbau. Die übrigen deutschen Autohersteller setzen zwar ebenfalls auf Zellforschung, kaufen die Zellen jedoch bei Lieferanten, zumeist aus Asien. BMW baut für die zylindrischen Zellen der neuen Klasse ein Montagewerk im bayrischen Irlbach-Straßkirchen. Audi hat für die Modelle der PPE-Plattform (A6/Q6) eine Montage im Stammwerk in Ingolstadt errichtet.
Hier werden zunächst Pouch-Zellen von CATL, später auch von anderen Lieferanten verwendet. Im Obergeschoss der Halle stehen mehrere Fertigungslinien, auf denen pro Tag 1.000 Batterien gefertigt werden. Hier arbeiten 300 Menschen in drei Schichten, dabei liegt der Automationsgrad bei 90 Prozent. Insgesamt 72 Roboter sind im Einsatz. Im ersten Schritt füllen Roboterarme blaue, flüssige Thermalpaste in den Batterierahmen. Auf diese Paste drücken Roboter die Batteriemodule. In einem Modul stecken 15 prismatische Zellen. In eine Batterie mit 83 kWh Kapazität kommen zehn, mit 95 kWh 12 Module. Sie werden mit dem Rahmen verschraubt. Im nächsten Arbeitsschritt ist Handarbeit gefragt. Mitarbeiter verlegen die Niedrigvolt-Kabel, mit denen Informationen aus den Modulen an das Batteriemanagement übertragen werden. Auch die Hochvolt-Konnektoren werden platziert, aber noch nicht mit den Modulen verbunden. Schließlich kommen die Zellen zu knapp 40 Prozent geladen in der Montage. Aus Sicherheitsgründen stellt später ein Roboter die Verbindung der Konnektoren zu den Zellen her. In der Batterie liegt eine Spannung von 800 Volt an.
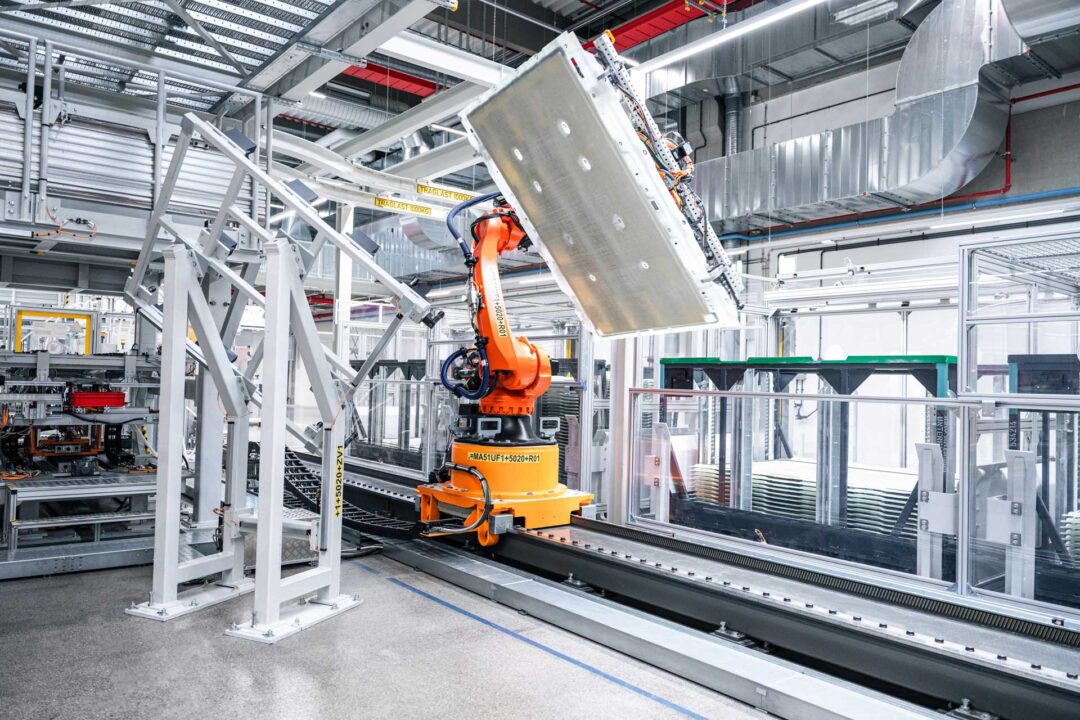
Zwei weitere Roboter tragen zwei parallele Linien Butyl auf. Die heiße Kautschuk-Dichtmasse sorgt für eine wasserdichte Verbindung zwischen Rahmen und Batteriedeckel. In den Deckel schrauben Roboter insgesamt 82 Schrauben. Zehn weitere Schraubverbindungen sind für die Befestigung im Auto vorgesehen. Nachdem der Deckel verschraubt ist, wird der Batteriemanagement-Controller (BMC) aufgesetzt. Er sorgt für die gleichmäßig Be- und Entladung der Zellen. Bei Ungleichgewichten führt er einen Spannungsausgleich durch. Hier wird auch die Temperatur in den Modulen erfasst. Die leichte Erhöhung auf der ansonsten flachen Batterie verschwindet später unter der Rückbank des Fahrzeugs. Im letzten Schritt wird an den Unterboden der Batterie ein Schutzschild aus Fiberglas geschraubt. Es verhindert das Eindringen von Fremdkörpern, die auf der Straße liegen oder bei einem Unfall gegen den Unterboden schleudern.
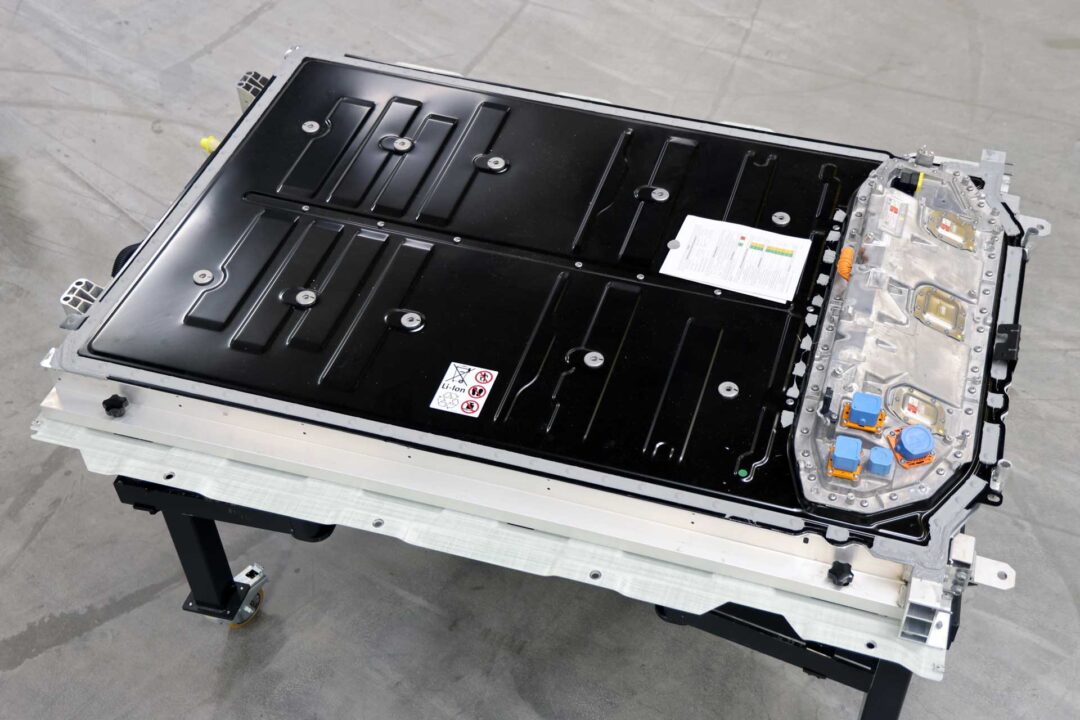
Batterie im Crash-Test
Wie sich ein E-Auto bei einem Unfall verhält, untersucht Porsche ebenfalls in Weissach. In einem weiteren Gebäude befindet sich das Crash-Testcenter. Die Halle ist rund 700 Meter lang. Fahrzeuge werden per Seilzug auf einem so genannten Flying Floor auf bis zu 120 km/h beschleunigt. Auf diesem Schlitten steht ein Macan, kurz nach einem Crash-Test. „Wie man sieht, hat die Batterie beim Aufprall praktisch keinen Schaden genommen“, sagt Simon Maurer, Governor des Sicherheitssystems Porsche Cayenne & Macan. Kurz zuvor ist das E-Auto mit 32 km/h seitlich schräg gegen einen abgerundeten Stahlpfeiler geprallt, der an einen 120 Tonnen schweren Betonblock montiert ist. Das Szenario stellt den Aufprall eines schleudernden Fahrzeugs gegen einen Baum nach. Natürlich überrascht die niedrige Aufprallgeschwindigkeit. „Die Geschwindigkeit ist durch die Unfallforschung statistisch belegt und repräsentiert einen schweren Feldunfall. Fahrer bremsen in letzter Sekunde und auch während das Fahrzeug in Richtung Baum rutscht, verlangsamt das Auto“, sagt Maurer. Neben Verformungen an Karosserie und Batterie interessiert die Ingenieure, ob alle Abschaltungen beim Unfall funktionieren. Melden die Sensoren einen Aufprall werden automatisch die E-Motoren sowie weitere Verbraucher entladen und von der Hochvoltbatterie getrennt.
Weiterlesen bei Golem.de
